When I was doing research and development with the Future Energy Electronics Center (FEEC) at Virginia Tech, some of my work was impeded by underdeveloped simulation models of the fuel cells we were testing. The models lacked certain key features of the fuel cell’s operation that caused my voltages and currents to be skewed, throwing off my power electronics tests.

To resolve this, I collected simulation data from the Ballard Nexa fuel cell system that we were using. Notably, I observed that:
- the parasitic losses from the system’s controls,
- the voltage overshoot and undershoot in transient conditions, and
- the temperature-dependent effects on fuel cell voltage
were not incorporated into the existing model. As such, I isolated the data that I could use to predict the behavior of these 3 phenomena and performed mathematical analysis like linear regression to identify key characteristics of their behavior.
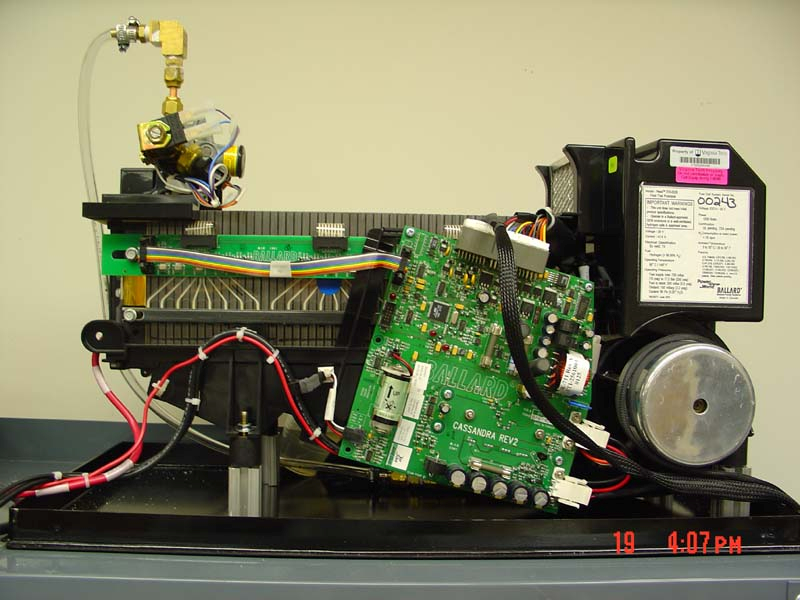
However, before adding them to the model, I noted that the choice of model elements played a big role in the model performance. That is, I had a number of circuit elements that I could have used to add these 3 features to the model, but the simplest – and therefore, fastest-simulating – circuit element would be the best. The resulting model modifications were implemented into the PSpice simulation; an example of the temperature-dependent addition is shown below.
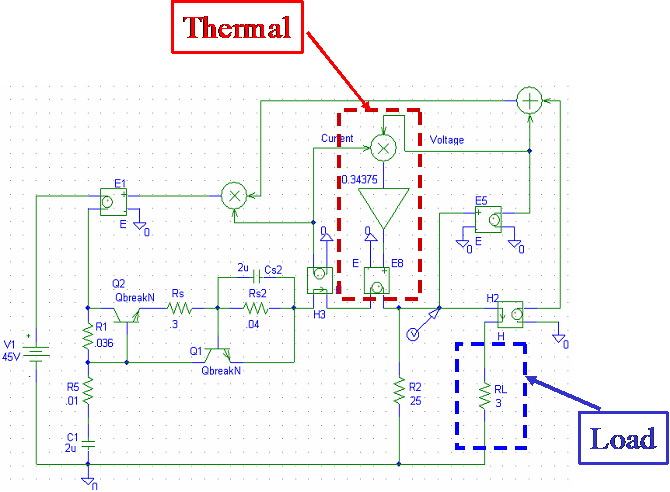
After the model was updated, a test was performed on the Ballard Nexa fuel cell system and then simulated via the PSpice model. As can be seen below, the simulation tracks key dynamic performance features of the fuel cell, as desired.
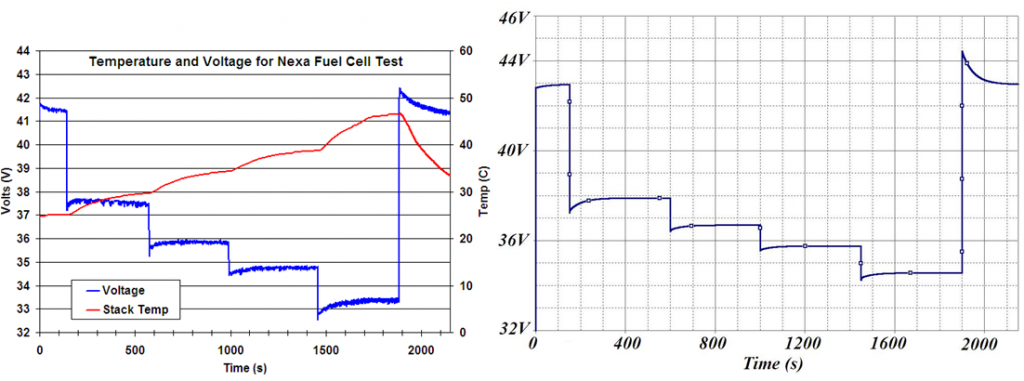
The results of this work were used in many ways. The model improvements directly benefited the power electronics design work that we were doing for our automotive applications of fuel cell systems.
As well, this project was the basis for my PhD qualifying exam in Electrical Engineering** at Virginia Tech. The Powerpoint presentation can be seen below.
Finally, I published these results at an international conference in Recife, Brazil, in 2005. The paper can be found at this link.
And, as luck would have it, my work caught the attention of the Chief Engineer of Honda Motors, who attended my presentation. Thankfully, I had been learning Japanese and was able to hold a basic conversation with him after my presentation, where he asked to meet with me later that evening for some social time. What an honor!
** = note: I did not complete this PhD, but rather switched into Engineering Education when it became available in 2007. I subsequently became the first student to complete the Engineering Education PhD program at Virginia Tech.